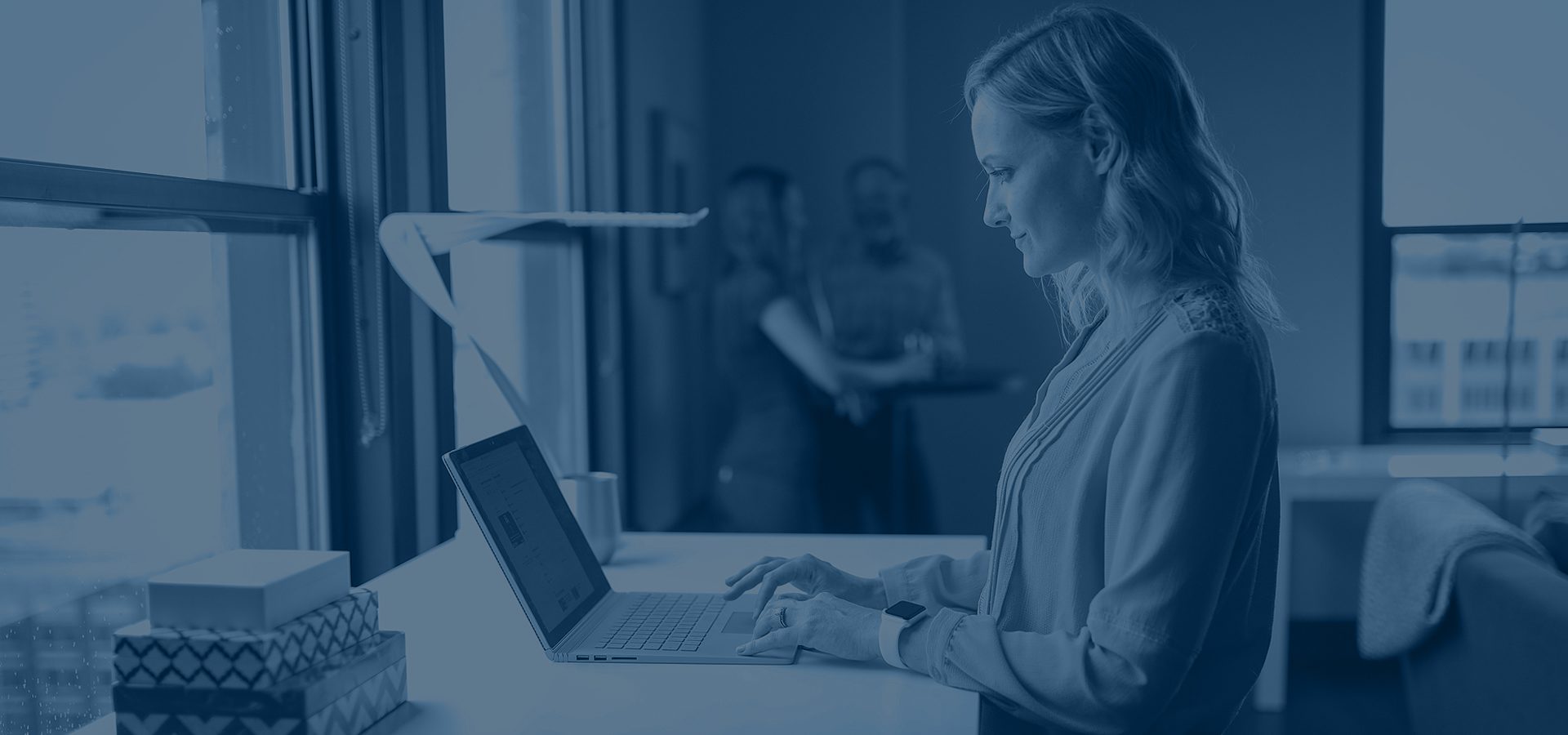
Navigating the ISO 13485 Audit Process: Ensuring Quality in Medical Device Manufacturing
In the realm of medical device manufacturing, adherence to stringent quality standards is paramount. ISO 13485, an international standard specifically designed for the medical device industry, outlines the requirements for a Quality Management System (QMS). Successfully navigating the ISO 13485 audit process is not just a compliance necessity but a commitment to delivering safe and effective medical devices. Let’s delve into the key aspects of this audit journey.
Understanding ISO 13485: A Foundation for Quality
ISO 13485 sets the foundation for a robust QMS tailored to the unique needs of medical device manufacturers. Compliance with this standard demonstrates a commitment to maintaining the highest levels of quality and regulatory compliance throughout the product lifecycle.
Initiating the ISO 13485 Audit Process: Key Steps
1. Preparation and Planning:
The audit journey begins with meticulous preparation. Identify key processes and areas within the organization covered by ISO 13485. Plan the audit scope, objectives, and criteria, considering the specific context of the organization and the regulatory landscape.
2. Internal Audit:
Conducting an internal audit before the formal ISO 13485 audit is a proactive step. This internal review helps identify areas of non-compliance or improvement opportunities. Addressing issues internally positions the organization for a smoother external audit.
3. Selection of Certification Body:
Choose a reputable certification body accredited for ISO 13485. Ensure that the certification body’s auditors possess the necessary expertise in medical device manufacturing and compliance.
4. Stage 1 Audit (Documentation Review):
The initial stage involves a review of documentation, ensuring that the organization’s QMS aligns with ISO 13485 requirements. This phase assesses the readiness of the organization for the formal audit.
5. Stage 2 Audit (On-Site Evaluation):
The on-site evaluation involves a comprehensive examination of processes, procedures, and practices. Auditors assess the effectiveness of the QMS implementation and its alignment with ISO 13485. Any non-conformities identified are documented.
6. Closing Meeting:
A closing meeting is held to discuss the audit findings. If non-conformities are identified, the organization receives a corrective action plan to address them.
7. Certification Decision:
Based on the audit findings and corrective actions, the certification body makes a decision regarding ISO 13485 certification. If compliance is confirmed, the organization is awarded ISO 13485 certification.
Challenges and Best Practices:
Challenges:
- Document Control: Ensuring effective document control is a common challenge. All relevant documents must be maintained, accessible, and regularly updated.
- Risk Management: Meeting ISO 13485’s risk management requirements can be complex. Identifying and addressing potential risks in product development and manufacturing processes is critical.
Best Practices:
- Training and Awareness: Regular training and awareness programs ensure that employees understand and adhere to ISO 13485 requirements.
- Continuous Improvement: Embrace a culture of continuous improvement. Regularly review processes, seek feedback, and implement enhancements to the QMS.
Conclusion: A Commitment to Excellence
Successfully navigating the ISO 13485 audit process is a testament to an organization’s commitment to producing safe and high-quality medical devices. Beyond achieving certification, organizations must embed a culture of quality, compliance, and continuous improvement to thrive in the dynamic landscape of the medical device industry. With ISO 13485 as a guiding framework, manufacturers can not only meet regulatory requirements but also exceed customer expectations in delivering life-changing and life-saving medical innovations.
Contact MG Environmental Consulting for their expertise and unwavering customer support to get you ISO 13485 certified.